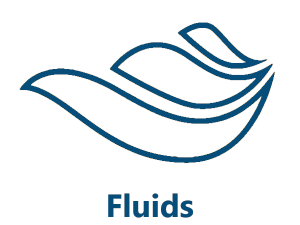
Computational fluid dynamics (CFD) is a tool with amazing flexibility, accuracy and breadth of application. Ansys CFD goes beyond qualitative results to deliver accurate quantitative predictions of fluid interactions and trade-offs. These insights reveal unexpected opportunities for your product — opportunities that even experienced engineering analysts can miss. While Ansys CFD empowers experienced analysts to deliver deep insights, serious CFD is not just for experts modeling rocket ships and racing cars. Engineers at every level across diverse industries are getting great value from CFD analysis.
APPLICATIONS
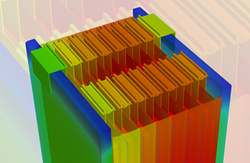
Battery Simulation
Chemistry, electricity and thermal management of batteries operate in a complex interplay that must be controlled within narrow margins to ensure long battery life and low cost. The slightest deviations from these margins can lead to dramatically shortened battery life – and to serious safety hazards. Cells are vulnerable to overheating from rapid discharging, overcharging or excessive ambient heating. Such overheating and uneven temperature distribution can lead to rapid cell degradation and shorten battery life. ANSYS helps maximize performance and safety while reducing cost and testing time.
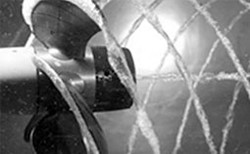
Cavitation
Cavitation happens when vapor bubbles form in a liquid because flow dynamics cause the local static pressure to drop below the vapor pressure. Without accurate prediction of cavitation, users cannot effectively optimize designs and set operating parameters and limits, potentially exposing their products to unexpected vibration and damage.
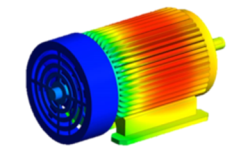
Electric Motor Cooling
For electrical components to be reliable and efficient, temperatures must be monitored and maintained within tight parameters. In electric motors, during the process of converting electrical energy to mechanical energy, heat is produced. This heat directly impacts the magnetic material temperature, which can reduce efficiency, overheat and demagnetize permanent magnets, and cause structural deformation which will increase noise and vibrations. ANSYS simulation solutions can be used in electrical, mechanical and thermal domains to optimize the design in electric motors.
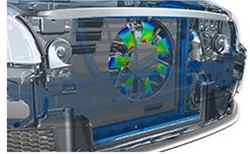
Fluid–Structure Interaction
Fluid flow exerts pressure on solid objects and deforms them. That deformation can, in return, impact the fluid flow around the object. ANSYS multiphysics accurately captures the interplay of these forces so you can optimize your product’s performance.
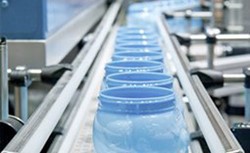
Rheology
Engineers need to optimize processes such as extrusion, thermoforming, blow molding, glass forming, fiber drawing and concrete shaping. CFD accelerates design while shrinking energy and raw material demands to make your manufacturing processes more cost-effective and environmentally sustainable.
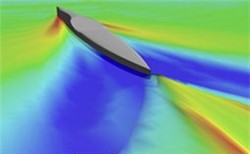
HPC – Fluids
ANSYS HPC enables CFD engineers to better simulate product performance and integrity in less time. In addition to efficiently scaling CFD solvers to a world record 172,000 cores, ANSYS has been investing heavily to ensure the entire CFD process, from prep to meshing to post-processing, is taking advantage of HPC to accelerate the total time to solution.
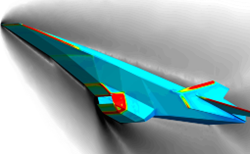
Hypersonics
Hypersonic speed occurs above Mach 5. As aircraft begin to travel above Mach 1, fluid flow changes, leading to very strong shocks, plasma, ablation, structural deformation, and chemical and thermodynamic nonequilibrium. Simulation is the best and most cost-effective way to accurately examine these challenges.
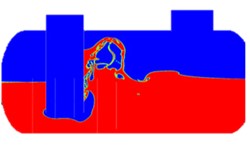
Multiphase Flows
Chances are that your fluids simulation includes multiphase flows like boiling, cavitation, dispersed multiphase flows, immiscible flows and flows with particulates. ANSYS CFD provides the widest range of sophisticated turbulence and physical models to accurately simulate the toughest challenges so you can confidently predict your product’s performance.
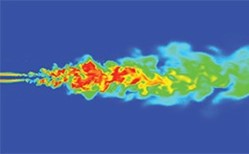
Reacting Flows and Combustion
Understanding and predicting the effects of reacting flows is critical to developing competitive products in diverse industries such as transportation, energy generation and materials processing. Knowing the underlying chemistry and physics enables designers of gas turbines, boilers and IC engines to increase energy efficiency and fuel flexibility and reduce emissions. Similarly, designers of high-throughput materials and chemical processes need high yields and quality, along with minimum byproducts and waste. A thorough grasp of the underlying physics and chemistry is also critical to making improvements in lithium-ion batteries, fuel cells and many other products.
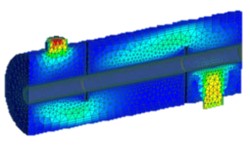
Reduced-Order Models
Reduced-order models (ROM’s) can accelerate your simulation time without sacrificing accuracy compared with a full 3D simulation. ROMs are simplified versions of a model that preserve essential behavior and dominant effects, for the purpose of reducing solution time or storage capacity required.
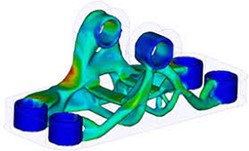
Shape Optimization
Instead of guessing geometry parameters and simulating hundreds of design points, ANSYS smart shape optimization tools give fast, specific insight into finding the ideal solutions for problems such as reducing pressure drop, optimizing drag, lift or heat transfer. For example, the ANSYS Adjoint Solver recommends and even automatically implements design enhancements, morphs the mesh to a more optimal shape and predicts the performance improvement.
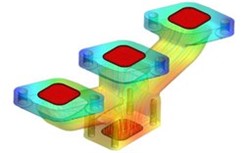
Thermal Management
Devices need to optimize heat transfer between fluids and solids to maintain a constant temperature and maximize performance, reduce maintenance costs and extend the life of the machine. Fluids can cool and heat machine parts, process equipment, engine components and other solids. These thermal effects can in turn deform the walls or parts that are being cooled or heated. ANSYS delivers fast and accurate solutions to predict performance for the widest range of fluid-solid heat transfer problems, including conjugate heat transfer (CHT) and thermal fluid–structure interaction (FSI).
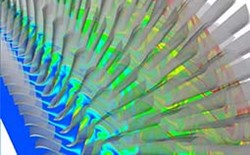
Turbomachinery
Turbomachinery is the most rewarding and the most challenging of simulations. ANSYS delivers innovations at every stage of the simulation process, from modeling to meshing, solving to post-processing. Whether designing a jet engine, wind turbine or turbocharger, ANSYS helps you to extend the limits of what is possible so you can maximize your product’s performance and efficiency.
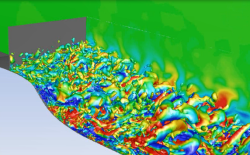
Turbulence Modeling
There is no single best turbulence model. Learn how turbulence model selection can impact simulation accuracy — even for seemingly simple applications. Turbulence is a critical computational fluid dynamics (CFD) app that you must get right.
PRODUCTS
Ansys Fluent
This powerful computational fluid dynamics (CFD) tool delivers fast, accurate results across the widest range of CFD and multiphysics applications. Accomplish more in less time and with less training with the New Fluent Experience.
Ansys CFX
Ansys CFX is a high-performance computational fluid dynamics (CFD) software recognized for its outstanding accuracy, robustness and speed with turbomachinery such as pumps, fans, compressors, and gas and hydraulic turbines.
Ansys Chemkin-Pro
Fast, accurate combustion and reacting flow simulations help achieve performance and fuel-efficiency goals cost-effectively. Chemkin-Pro reduces chemistry analysis time by orders of magnitude without sacrificing accuracy
Ansys Forte
Fast, accurate simulation for internal combustion engines and positive-displacement compressors.
Ansys FENSAP-ICE
Advanced simulations of in-flight ice accretion, ice protection system analysis, aerodynamic penalty and ice shedding for aircraft and turbomachinery.
Ansys Polyflow
Ansys Polyflow provides advanced fluid dynamics technology for companies in the polymer, glass, metals and cement processing industries.