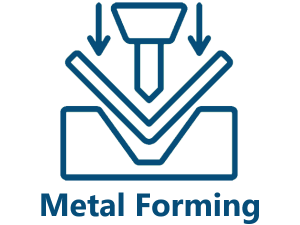
Metal forming simulation helps many industries evaluate the performing of dies, processes and blanks prior to building try-out tooling. These solutions help determine whether a proposed product and tooling design will produce parts free of defects such as fracture, spring back or wrinkling. The technology is ideal for cost reduction, quality improvement and productivity gains.
APPLICATIONS
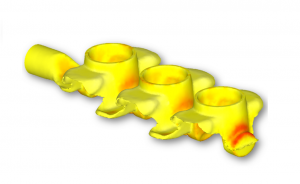
Hot forging
Applications cover the entire range of forged products. Axisymmetric (round) parts can be simulated, including turbine disks, flanges, upset tubes, shafts and more are routine applications. Three-dimensional applications include gears, crankshafts, connecting rods, pistons, control arms, tracks, yokes, medical implants and more. Simulation makes a significant improvement in development time and cost.
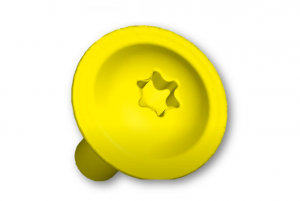
Cold forming
Applications such as fasteners, bearing components, spark plug bodies were reported in the early 1990’s. Due to the precision nature of the product, even very small defects can be a serious and expensive problem. Additionally, tool failures resulting from high forming pressure can be analyzed and eliminated using the powerful die stress analysis capability.
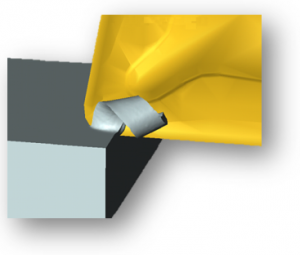
Machining
Our metal forming solution is the gold standard simulation tool, with the ability to simulate milling, drilling and even tapping!
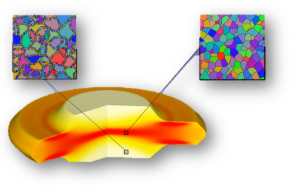
Heat treatment
We provide a leading simulation software in heat treatment and microstructure. It has been used by leading manufacturers in aerospace, automotive, energy and other fields. Research projects around the world have used our simulation as the preferred solution to heat treat simulations.
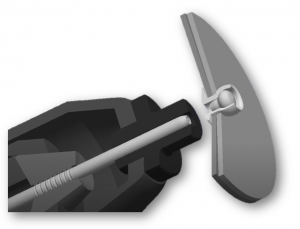
Mechanical joining
Complex forming operations such as rivets and staked fasteners are possible in both 2D and 3D simulations. Mechanical joining requires a robust FEM engine and mesh generator.
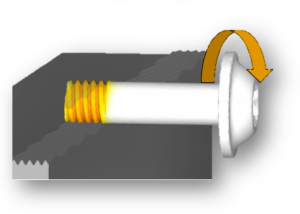
Rolling
Rolling applications range from ring rolling to shape rolling. Orbital forming, thread rolling, cross wedge rolling and other process are possible as well.
PRODUCTS
DEFORM
The DEFORM® system is an engineering software that enables designers to analyze metal forming, heat treatment, machining and mechanical joining processes on the computer rather than the shop floor using trial and error. Process simulation using DEFORM has been instrumental in cost, quality and delivery improvements at leading companies for two decades. Today’s competitive pressures require companies to take advantage of every tool at their disposal. DEFORM has proven itself to be extremely effective in a wide range of research and industrial applications. Scientific Forming Technologies Corporation (SFTC) develops and supports the DEFORM System. SFTC is available for consulting, training, contract simulation and software development on a project basis.